How Material Selection Affects CNC Machining Outcomes
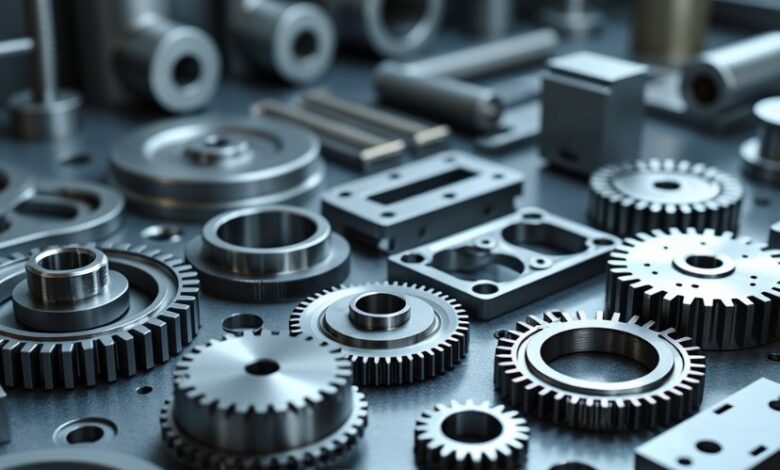
Material selection plays a crucial role in determining the success of CNC machining processes. The type of material used can impact everything from machining speed and tool wear to final product quality and cost. By understanding how different materials behave during machining, manufacturers can make informed decisions that optimize production efficiency, reduce waste, and enhance product performance. This guide will explore the key ways in which material selection affects CNC machining outcomes, along with strategies to ensure optimal results.
Material Properties and Machinability
One of the most significant factors in CNC machining is machinability, which refers to how easily a material can be cut, shaped, and finished by machining tools. Materials with poor machinability may cause excessive tool wear, increase production time, or lead to rough surface finishes. Some of the key properties that determine machinability include:
- Hardness: Harder materials, such as stainless steel and titanium, are more difficult to machine as they resist cutting, leading to faster tool wear and increased production costs.
- Tensile Strength: Materials with high tensile strength, like certain aluminum alloys, require more force during machining, affecting tool life and machine performance.
- Thermal Conductivity: Materials with low thermal conductivity can retain heat during machining, causing thermal expansion, tool wear, and dimensional inaccuracies.
- Ductility: Ductile materials, such as copper and plastics, can easily deform during machining, affecting precision.
Machinability ratings for common materials are typically used to predict how a material will respond to CNC machining, allowing manufacturers to choose the most suitable materials for their projects.
Tooling Considerations Based on Material
Different materials require different types of cutting tools and machining strategies to ensure efficiency and precision. For instance, cutting tools for hard materials like steel or titanium need to be more wear-resistant and durable, often made from carbide or coated with diamond-like carbon. In contrast, softer materials like aluminum or plastic may require less aggressive cutting tools, reducing costs.
Some materials also demand specific cutting speeds and feeds to prevent excessive heat buildup or tool breakage. For example, machining stainless steel may require slower speeds but higher feeds, whereas machining aluminum benefits from higher speeds and lower feeds. Choosing the right tooling is essential to optimizing CNC machining outcomes.
Surface Finish and Tolerance
The quality of a CNC-machined part is often measured by its surface finish and dimensional accuracy. Material selection directly influences these factors:
- Surface Finish: Harder materials, such as steel, tend to produce rougher surfaces unless advanced finishing processes like polishing or grinding are used. Softer materials, like aluminum or brass, naturally result in smoother finishes during CNC machining.
- Tolerance Levels: Materials with greater dimensional stability, such as certain plastics and metals, maintain tighter tolerances during machining. This ensures that the final product conforms to precise specifications, especially in industries like aerospace and medical device manufacturing.
For projects where high precision is critical, selecting a material that offers good machinability and dimensional stability is essential.
Material Cost vs. Performance
In CNC machining, balancing material cost with performance is a common challenge. High-performance materials like titanium or advanced composites offer superior strength, corrosion resistance, or lightweight properties but come at a higher cost and may be more challenging to machine.
On the other hand, more affordable materials like aluminum or certain plastics offer easier machinability and lower tool wear, making them ideal for high-volume production or less demanding applications. The decision on material selection should take into account the specific requirements of the project, such as strength, weight, durability, and cost-efficiency.
At Yijin Hardware, we prioritize the importance of balancing material selection with project requirements to deliver cost-effective CNC machining solutions without compromising on quality. By tailoring the choice of materials to the unique needs of each project, we ensure optimal results while minimizing production costs and time.
Impact on Machining Time and Efficiency
Material selection has a direct impact on machining time and overall efficiency. Softer materials like aluminum or brass can be machined faster than harder materials like steel or titanium, reducing cycle times and improving productivity. However, machining harder materials may require more tool changes, slower cutting speeds, and longer production times to maintain part quality.
Additionally, the machinability of materials can influence the choice of machining strategies, such as the use of roughing or finishing passes, as well as the selection of coolant systems to prevent heat buildup.
Read also: How handheld technology is revolutionising gambling on the go
Material-Specific Challenges
Each material comes with its unique set of challenges that must be addressed during the machining process:
- Metals: Metals like steel, aluminum, and titanium are commonly used in CNC machining, but each has distinct properties that affect machining outcomes. For example, aluminum is highly machinable but prone to chip buildup, while steel is harder to machine but offers excellent strength and durability. Titanium, while lightweight and strong, presents challenges with heat generation and tool wear.
- Plastics: Plastics like ABS, nylon, and polycarbonate are lightweight and easy to machine, making them ideal for prototype development and low-stress applications. However, they can warp or deform under heat, requiring careful temperature control during machining.
- Composites: Advanced composites, such as carbon fiber, are increasingly used in industries like aerospace and automotive for their lightweight and strength properties. However, they are challenging to machine due to their abrasive nature, which can wear down tools quickly.
Read also: The Technology Powering Trading Signals in Binary Options: a Deep Dive
Strategies for Optimizing Machining Outcomes
To optimize CNC machining outcomes based on material selection, manufacturers should consider the following strategies:
- Material Testing: Conducting material tests before full-scale production can help identify potential machining challenges, such as tool wear, thermal expansion, or surface finish issues.
- Tooling Optimization: Selecting the right cutting tools, coatings, and machine settings for the specific material can improve machining efficiency, reduce costs, and extend tool life.
- Machining Environment Control: Using proper cooling systems, such as flood coolant or air blast, can help manage heat buildup, especially when machining harder materials like titanium or steel.
- Advanced Finishing Techniques: For materials that require superior surface finishes, techniques like grinding, polishing, or anodizing can be applied after machining to achieve the desired result.
Conclusion
Selecting the right material for CNC machining is essential for achieving high-quality results. By understanding how material properties like hardness, thermal conductivity, and machinability affect the process, manufacturers can make informed choices that optimize production efficiency and part performance. Whether working with metals, plastics, or composites, the right material selection can significantly improve machining outcomes, reduce costs, and enhance product quality.