Pneumatic Cylinder Efficiency: How to Maximize Productivity in Industrial Automation
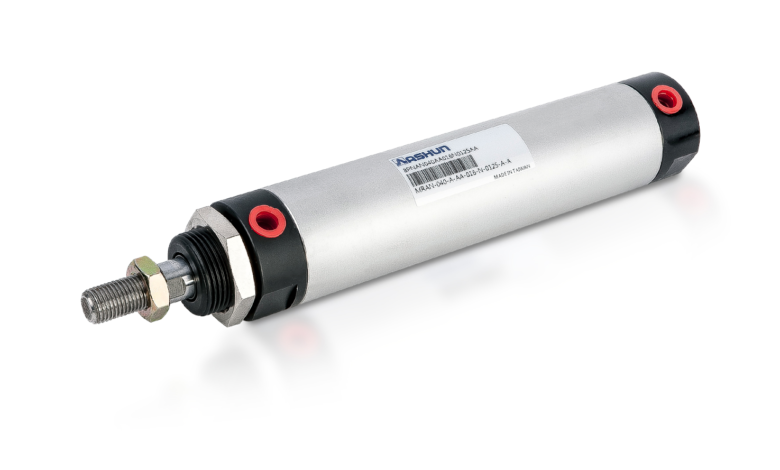
In today’s cut-throat industrial environment, every company looks forward to searching for various means of increasing the productivity of operations while controlling the costs of production. Another very integral part of the industrial automation system is the pneumatic cylinder. That is why any improvement in the industry associated with pneumatic cylinders and their efficiency will always enhance productivity and overall system performance. The strategies to enhance the effectiveness of pneumatic cylinders and optimization productivity in automated industries will be discussed here in this article.
Assess Current Cylinder Performance
When making these kinds of investments, it is only wise that you assess the existing performance level of your pneumatic cylinder. It also enables firms to reduce cost by not finding all possible wastes that need to be addressed but to concentrate on those areas that would bring improvements to productivity most.
Key Performance Indicators to Assess:
– Air consumption: Find out how much compressed air your pneumatic system is consuming. This is very evident if there is excessive air consumption, which must be less throughout the process.
– Cycle times: Any cycle range other than the fluid possible speeds might present inside a cylinder and disturbances should be evident in terms of slow cylinders cycle or inconsistency of movement that could be linked to friction or interior deterioration.
– System pressure: There is usually a check to ensure that the system is running at pressures higher than it should be, in regard to energy waste and cylinder deterioration.
It’s best to seek the services of the manufacturer of pneumatic cylinders who specializes in the efficient units that allow you to upgrade your company from outdated low-efficiency units to the top models that demand less air consumption and offer better control.
Choose the Right Cylinder Type
It is well understood just how vital it is to choose the correct pneumatic cylinder in the productive automation milling system and this comes because of the different types of tasks that the automation system does at its job. As mentioned previously there are different kinds of cylinders and each has its own benefits depending on their usage.
Common Cylinder Types:
– Single-acting cylinders: In the case of air pressure, one could turn the piston by forcing it to move in one direction with the assistance of the spring to take it back to the original position. Good for installations that do not involve much shifting or vibration such as residential buildings with small footprints.
– Double-acting cylinders: Reverse force in both directions, and are therefore available for other more strict automation applications that calls for fine control and velocity.
– Rodless cylinders: Available in compact designs which makes the apparatus ideal for organizations that have limited space while at the same time has high efficiency.
Today, you can select from a range of cylinder types made by one of the first ten pneumatic cylinder producers and thus achieve the greatest productivity.
Optimize Air Supply Systems
Effective management of compressed air supply is as important to the performance of the pneumatic cylinders. It will be extremely difficult to run even the most technologically refined pneumatic cylinders efficiently if there is no proper control on the amount of air being input to the cylinders.
Ways to Optimize Air Supply:
– Install air regulators: These devices ensure thus that the system utilizes only the required amount of air pressure thus eliminating wastage of energy.
– Maintain clean, dry air: It is well understood that presence of moisture and debris in compressed air systems put a lot of strain on the pneumatic cylinders and has therefore the effects of causing wear and tear of these cylinders thus; making them less efficient.
– Use energy-efficient compressors: This can be obtained by replacing the existing mechanical compressors with more ‘’Smart’’, energy efficient compressors.
Discuss with your producer of pneumatic cylinders regarding your air supply systems so as to understand their efficiency regarding the specific demands of the automation processes without waste of resources.
Implement Predictive Maintenance Practices
The ways towards the enhancement of pneumatic cylinders lie in the proper ways towards the maintenance of the pneumatic cylinders. However, these regular service intervals could not reduce the likelihood of a sudden failure or drop in efficiency. The key point that should be said about this aspect is that the application of the predictive maintenance practices contributes to the increase in both the efficiency of a car and its reliability.
Benefits of Predictive Maintenance:
– Monitor real-time performance: The other benefit of sensors is that you will notice that the pneumatic cylinders begin to wear, leak, or work inefficiently before you are completely aware of the same.
– Extend cylinder lifespan: Preventive measures like early detection of friction or leakage help in avoiding early cylinder failure of the equipment and hence increase the usable life of equipment.
– Reduce downtime: It eliminates instances where the automation systems could be offline thereby reducing productivity.
The majority of the leading players in the pneumatic cylinder market have started featuring smart or sensor integrated cylinders that facilitate the real time vital performance data making the concept of predictive maintenance more effective.
Optimize Cylinder Design and Customization
Thus, order-based building to acquire pneumatic cylinders can increase efficiency and productivity of the cylinders even more for different applications. Standard designs may not necessarily solve more complicated automation systems and designs that are tailored for specific needs may be more effective.
Customization Options for Efficiency:
– Stroke length adjustments: Cylinders having accurate values for stroke lengths control wastage of air and enhance the speed of working.
– Lightweight materials: If lightweight materials for instance aluminum are used it is possible to decrease the amount of force needed to move cylinder, hence decrease the rate of air consumption.
– Sealing improvements: This way, there are very few chances for leak and hence, constant pressure for long term efficiency is maintained.
The reason is that partnering with a company that supplies pneumatic cylinder manufacturers that provide solutions for customization of your cylinders will mean that the pneumatic cylinders designed will be custom made to suit your automation system thus enhancing the functions and durability of the cylinders.
Optimisation of the pneumatic cylinder is a very crucial element in enhancing productivity of industrial automation systems. Determining cylinder performance, selecting the correct type of cylinder, improving air supply systems, conducting predictive maintenance, and engaging high-quality custom made cylinders will help B2B companies improve their automation line to a great extent.
Working with top 10 pneumatic cylinder manufacturers means availability of novelties in cylinder design and high quality customized components. If acute strategies are employed in your business then your business will be efficient and productive, and costs will be low while in the industrial business environment you will be the winner.