45,000 Square Meters of Excellence: Deermaple’s Manufacturing Process
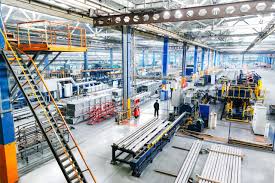
Deermaple is a brand known for its innovative outdoor gear, and much of this success is attributed to the meticulous manufacturing process behind each product. With over 45,000 square meters of dedicated manufacturing space, Deermaple has created an environment where quality and precision are prioritized in every stage of production. From designing durable Wood Stove to creating other high-quality camping equipment, the company’s commitment to excellence is evident in its attention to detail. In this article, we’ll dive deep into how Deermaple’s expansive manufacturing process ensures the creation of reliable and top-performing outdoor gear.
A State-of-the-Art Manufacturing Facility
Deermaple’s impressive 45,000 square meters of manufacturing space is designed to accommodate the complex production of outdoor gear. The facility is divided into various sections that specialize in different stages of manufacturing. From raw material handling to the final inspection, each section is equipped with advanced technology to optimize production efficiency and product quality. The layout of the manufacturing facility allows for streamlined processes, ensuring that the company can meet demand without compromising on the precision and durability that customers expect from Deermaple products.
The manufacturing process begins with the careful selection of materials, which is the foundation of Deermaple’s reputation for producing high-quality wood stoves and other camping gear. By utilizing state-of-the-art equipment, the company ensures that raw materials are processed with accuracy and care, giving rise to products that are not only reliable but built to last. The 45,000 square meter space is designed to allow for maximum production flexibility, which enables Deermaple to cater to various customer needs while maintaining high standards.
Precision in the Design of Wood Stoves
Wood stoves are one of Deermaple’s signature products, known for their efficiency, portability, and durability. The design and manufacturing of these stoves involve a rigorous process to ensure that each stove meets high performance and safety standards. At the heart of the production process is the precise engineering of components. Deermaple’s team of designers and engineers use advanced CAD software and simulation tools to develop detailed blueprints, ensuring that every part of the stove is designed for optimal performance.
Once the design is finalized, the components are fabricated using advanced machinery. The wood stoves are constructed with materials such as high-quality stainless steel, which provides exceptional heat resistance and durability. The manufacturing facility is equipped with cutting-edge machines that are capable of handling the intricacies of crafting these complex components, ensuring that each piece fits together perfectly. Whether it’s the stove body, the door seals, or the flue system, every part is produced with a focus on precision and longevity.
Advanced Manufacturing Techniques
Deermaple employs a range of advanced manufacturing techniques to ensure that their products meet the highest standards of quality. One of the key processes is the use of laser cutting technology, which allows for extremely precise cuts in metal components. This is especially important in the production of wood stoves, where accuracy is crucial for ensuring that the stove operates efficiently and safely. Laser cutting helps to minimize material waste, making the process both efficient and cost-effective.
In addition to laser cutting, Deermaple utilizes robotic welding systems to ensure that all parts are welded securely and consistently. This technology helps to improve the overall quality of the product by eliminating human error and ensuring uniformity in every weld. The robotic welders are programmed to follow exact specifications, ensuring that the structural integrity of each stove is maintained throughout the manufacturing process. These advanced techniques not only enhance the quality of the final product but also reduce the time needed for production, allowing Deermaple to meet growing customer demand.
Quality Control at Every Stage
Deermaple is committed to ensuring that every product leaving the manufacturing facility meets the highest standards of quality. The company employs a rigorous quality control process that involves multiple checks at various stages of production. From the initial inspection of raw materials to the final testing of the finished product, quality control is an integral part of the manufacturing process. This ensures that Deermaple’s wood stoves and other outdoor products are built to last and perform as expected in even the most challenging environments.
At the beginning of the production process, raw materials are thoroughly inspected to ensure they meet Deermaple’s strict quality standards. Throughout the manufacturing process, each component is carefully checked for defects, and any issues are addressed immediately. Once the wood stove is fully assembled, it undergoes a series of rigorous tests, including heat resistance tests, structural integrity checks, and functional assessments. These tests ensure that the stove is safe to use and that it operates at optimal efficiency. Only after passing these tests does the product move on to the final stage: packaging and shipment.
Sustainability and Eco-Friendly Manufacturing Practices
As a company that values sustainability, Deermaple integrates eco-friendly practices into its manufacturing process. The use of renewable energy sources and waste reduction initiatives are core principles in Deermaple’s production philosophy. The company has made significant investments in energy-efficient machinery and processes that reduce the environmental impact of production. For example, the laser cutting and welding processes are optimized to minimize energy consumption while maintaining high production standards.
In addition to energy efficiency, Deermaple places a strong emphasis on reducing material waste. The company uses advanced software to optimize material usage, ensuring that raw materials are used efficiently and that any scraps are minimized. Recycled materials are also incorporated into the production of certain components, further reducing the environmental footprint of manufacturing. By prioritizing sustainability in its manufacturing process, Deermaple is not only creating high-quality products but also contributing to the protection of the environment.
Logistics and Distribution: Delivering Products Worldwide
Once the products are manufactured and undergo quality control, Deermaple ensures that they are delivered to customers in a timely and efficient manner. With a global customer base, the company has established a streamlined logistics and distribution process to ensure that its products reach outdoor enthusiasts all around the world. The 45,000 square meter facility allows for effective inventory management, ensuring that products are readily available for shipment when orders are placed.
Deermaple’s distribution network is designed to meet the demands of both retail and direct-to-consumer orders. Whether customers are purchasing wood stoves, camping furniture, or other outdoor gear, they can expect fast and reliable delivery. The company partners with trusted logistics providers to ensure that all products are safely and efficiently transported to their destination. This efficient logistics system is a key factor in Deermaple’s ability to maintain a strong presence in international markets, exporting their products to over 100 countries worldwide.
Innovation and Future Expansion
Deermaple’s commitment to excellence doesn’t stop at its current manufacturing processes. The company is constantly looking for ways to innovate and improve its products and production techniques. As the demand for outdoor gear continues to grow, Deermaple is investing in research and development to ensure that its products remain at the forefront of the industry. The company is also exploring new materials and technologies that will enhance the performance of its wood stoves and other outdoor equipment.
In addition to technological advancements, Deermaple is committed to expanding its manufacturing capacity to meet the growing needs of its customers. The company plans to further enhance its 45,000 square meter facility with additional production lines and upgraded equipment, allowing it to continue providing top-quality products while keeping up with the increasing global demand. As Deermaple continues to innovate and expand, customers can expect even more cutting-edge outdoor gear designed to enhance their camping and adventure experiences.
Conclusion
Deermaple’s 45,000 square meter manufacturing facility is a testament to the company’s dedication to quality, efficiency, and innovation. From the careful selection of materials to the advanced manufacturing techniques employed, every step of the process is designed to produce outdoor gear that meets the highest standards. Whether it’s a durable wood stove or other camping essentials, Deermaple’s commitment to excellence ensures that customers receive products that are built to last and perform under the most demanding conditions. By focusing on precision, sustainability, and continuous improvement, Deermaple is setting a new standard in the outdoor gear industry, making it a trusted name among adventurers around the world.