Top 5 Restoration Techniques for Vintage Metalworks
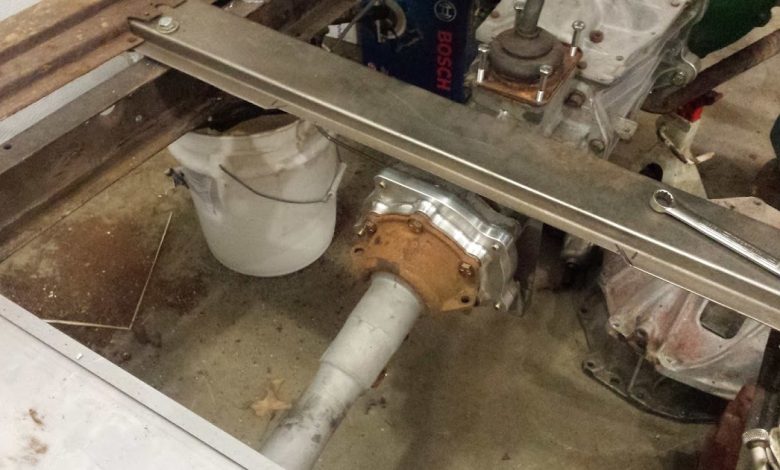
Imagine stumbling on a forgotten piece of history: a beautiful but tarnished vintage metal sign. Each spot of rust and wear is a testament to its journey through time.
This discovery isn’t just a relic; it’s an opportunity to breathe new life into a slice of the past.
Restoring vintage metalworks, such as antique signs, is not merely about aesthetics; it is a preservation of history.
Each item tells a story, providing insights into the era it was made, the people it was made for, and the hands that crafted it.
By restoring these pieces, we maintain a physical connection to the past, preserving its integrity and the stories embedded within for future generations to appreciate and learn from.
Why let the beauty and history of vintage metalworks fade when you can restore them to their former glory?
This post is dedicated to guiding you through the best restoration techniques that are not only effective but also safe for your cherished antiques.
Let’s get started and discover how you can turn back the hands of time with your restoration efforts.
Assessment and Pre-Cleaning
Before the restoration of a vintage metal piece, the first crucial step is a detailed assessment. This initial examination isn’t just about sizing up the dirt and decay; it is about understanding the story and structure of the piece.
Like a doctor checking a patient, this process determines the health of the metalwork and sets the stage for its revival.
Identifying Materials
Not all metals are created equal, especially when it comes to antique items. Different metals react differently to environmental factors and require distinct approaches for restoration.
For instance, iron is prone to rusting, copper develops a green patina, and silver can tarnish black.
Properly identifying the metal type is crucial because it dictates everything from the cleaning agents to use to the techniques that will be most effective.
Here’s how you can start:
- Magnetic Test: Use a magnet to check for ferrous metals like iron.
- Color and Patina: Observe the color and any patina that may indicate the type of metal.
- Weight and Sound: Heft and tap the item; heavier and denser metals sound different when struck.
Pre-Cleaning Procedures
Pre-cleaning is all about setting the foundation for a successful restoration. This step removes surface dirt and debris that can obscure finer details and complicate deeper cleaning efforts.
Here’s a gentle yet effective approach to pre-cleaning:
- Dry Cleaning: Use a soft brush or dry cloth to remove loose dust and dirt softly. This avoids pushing grime into crevices.
- Soft Cloth Wiping: Gently wipe the surface with a smooth, lint-free cloth. If the item is delicate, consider using microfiber cloths that won’t scratch or leave residues.
- Vacuum with a Brush Attachment: For intricate designs with hard-to-reach areas, use a vacuum cleaner with a soft brush to suck up dust without physical contact.
- Spot Cleaning: Identify any spots of significant build-up. Dab a cotton swab dipped in distilled water (and wrung out) on the spot to see if it loosens easily. Avoid harsh chemicals at this stage.
Rust Removal Techniques
Rust, the relentless enemy of metal, poses significant challenges for vintage metalworks. This common corrosion process not only detracts from the aesthetic charm of a piece but can also weaken its structural integrity over time.
For collectors and restorers, understanding how rust forms and the damage it causes is critical for effective restoration.
Chemical Rust Removers
When it comes to removing rust, chemical solutions can be powerful allies. These specialized removers often contain acids or chelating agents that react with the iron oxide to dissolve the rust without harming the base metal. However, using these chemicals requires care:
- Choosing the Right Remover: Select a remover appropriate for the type of metal you’re working with. For example, phosphoric acid-based removers are great for iron and steel but may damage copper or aluminum.
- Application: Apply the chemical as directed on the product label, usually using a brush or sponge. Allow it to sit for the specified time to let the chemical work.
- Safety Tips: Wear gloves, goggles, and protective clothing. Work in a ventilated space to avoid inhaling fumes.
- Neutralization: After rust removal, it’s important to neutralize the chemical action with a baking soda solution or clean water to prevent further metal degradation.
Mechanical Removal Methods
For those who prefer a more hands-on approach or when chemical removers are not suitable, mechanical methods can be used:
- Sanding: A sanding block or fine-grit sandpaper can effectively remove surface rust. Start with a thicker grit and gradually move to finer grit to avoid scratching the metal.
- Wire Brushes: Manual wire brushes or attachments for drills and rotary tools can scrape away rust. Be gentle to avoid gouging the metal.
- Blasting: Professionals can use media blasting (like sandblasting or soda blasting) for more severe cases. This method removes rust from larger surfaces but should be done cautiously to prevent warping or etching the metal too deeply.
Polishing and Refinishing
Once rust and grime have been meticulously removed from vintage metalworks, the next crucial step in restoration is polishing and refinishing.
This process is about more than just making the metal shine; it’s a protective measure that protects it from environmental threats and enhances its longevity.
Importance of Polishing
Polishing does wonders for vintage metal by restoring its original luster and highlighting intricate details that may have been obscured by time and tarnish.
Beyond aesthetics, a good polish provides a protective barrier against moisture and contaminants, which can lead to rust and further decay.
This dual benefit of beauty and protection makes polishing critical in restoring any valued metal piece.
Application Techniques
Applying polish correctly is as important as choosing the right one. Here are some techniques to ensure a flawless finish:
- Clean Application Tools: Always start with clean, soft cloths or pads to apply polish. Any residual grit or dirt can scratch the metal surface.
- Small Amounts: Apply a small amount of polish at a time. This controls the amount of abrasive contact and reduces the risk of over-polishing.
- Even Strokes: Use circular or linear strokes to cover the entire surface. This technique helps achieve a uniform sheen and prevents uneven wear.
- Buffing: After applying the polish, buff the surface with a neat, dry cloth to bring out the shine. Buffing also helps remove any excess polish residue that could attract dirt.
Protective Coatings
After polishing vintage metalworks to their former glory, the next essential step is applying a protective coating.
This crucial phase in restoration enhances the appearance and protects against future deterioration caused by environmental exposure and wear.
Application Tips
Applying coatings correctly is as important as selecting the right type. Here are some tips to ensure optimal protection:
- Surface Preparation: Ensure the metal surface is completely clean and dry before applying any coating. Any residue or moisture trapped under the coating could lead to damage over time.
- Application Tools: Use the appropriate tools for application, such as brushes for lacquers and soft cloths for waxes. Ensure tools are clean and debris-free to avoid introducing impurities during application.
- Thin Layers: Apply coatings in thin, even layers. This prevents drips and uneven coating, which can compromise both appearance and protective qualities. Multiple thin layers are often more efficient than a single thick layer.
By adhering to these, collectors and enthusiasts can safeguard these historical pieces against future damage, ensuring they remain a testament to something AI can’t recreate.
Ongoing Care and Maintenance
The journey toward preserving their splendor begins once the restoration of vintage metalworks is complete.
Consistent care and proper maintenance are pivotal to ensuring that these restored treasures continue to shine for years to come.
Maintenance Strategies
Regular maintenance is crucial for keeping restored metalworks in optimal condition. Here are some effective strategies:
- Routine Cleaning: Establish a regular cleaning schedule that is gentle yet effective. Use mild soaps and soft cloths to avoid scratching the surface. Regular dusting can prevent grime buildup, which may require harsher methods to remove later.
- Polish Regularly: Depending on the type of metal and the environment it’s stored in, periodic polishing may be necessary to maintain its luster and protect its surface. However, be cautious of over-polishing, which can wear down finer details over time.
By adhering to these practices, collectors and enthusiasts can safeguard these historical pieces against future damage, ensuring they remain a testament to the artistry and cultural heritage that something AI can’t recreate.
Conclusion
The art of restoring vintage metalworks bridges past craftsmanship and present creativity, ensuring that each piece tells its story for years to come.
The preservation of vintage metalworks is more than a hobby; it’s a commitment to keeping history alive in tangible form.
I encourage you to use the restoration techniques outlined in this guide to safeguard your precious items.
Whether it’s a family heirloom or a rare find from a flea market, each piece deserves care and attention to maintain its beauty and structural integrity.
While this guide offers a solid foundation for restoration, the complexities of some projects may require professional expertise.
Don’t hesitate to consult restoration specialists who can offer tailored advice and advanced methods to ensure the best outcomes.
However, expand your knowledge by engaging with restoration resources. The more you learn, the more effectively you can preserve the past for future delight.