Dust Grinders: Key Considerations for Efficient Mineral Processing
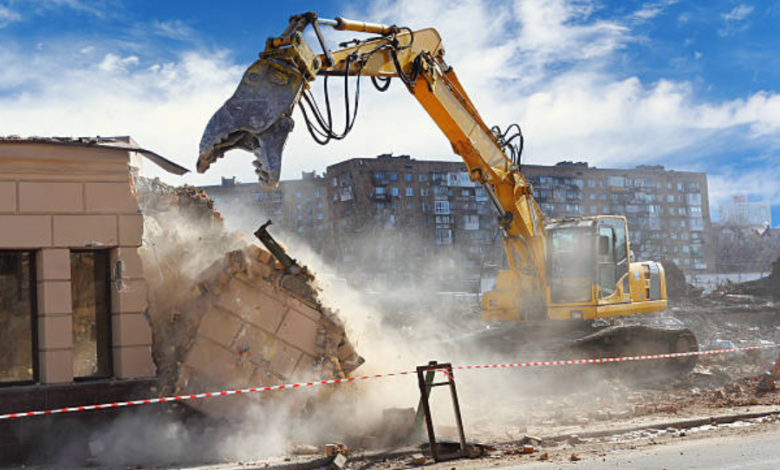
When it comes to mineral processing, close control and accuracy in every aspect of processing is crucial in attaining high yields and in making the process as cheap as possible. Dust grinders commonly referred to as “molinillo de polvo” are used to adjust the particle size of minerals and this has a direct impact on the subsequent processes such as the magnetic separators commonly known as “separadores magneticos”. This paper establishes the fundamental factors that relate to the dust grinder with an aim of achieving an optimal and a more efficient mineral processing.
Particle Size Distribution
The performance of dust grinders in mineral processing is therefore based mainly in achieving the right particle size. Uniformity of particle size also means that subsequent processing equipment such as the separadores magneticos will operate efficiently. The liberation of minerals is benefited by fine particles which are very important in the process of magnetic separation.
Getting the correct PSD therefore depends on the control of the grinding process. These are choosing the right type and size of the balls for grinding, controlling the grinder characteristics such as speed and pressure and setting up monitoring and controlling tools to oversee the process. It is still almost possible to get immediate feedback regarding their particle size distribution in the process of operation, with the aid of enhanced monitoring systems.
Uniform particle size also improves the effectiveness of separadores magneticos but at the same time eliminates chances of over grinding or under grinding which are major disadvantages that would have a knock down effect on the overall recovery of the minerals processed. There is also the inherent benefit of having particles of uniform size in the subsequent use of chemicals in floatation processes after having applied magnetic techniques that enhances recovery rates and at the same time, reduces the amount of chemicals used.
Read more: Elevating performance management and employee relations with an EOR
Efficiency and Throughput
The effectiveness of a dust grinder is not only a determinant of the quality of the produced minerals, but also a measure of the plant’s productivity. Such dust grinders are efficient in that they are capable of processing more quantities of materials in the same efficiency as the other but without affecting the quality of the dust that is to be produced. This capability is very important to plants that would wish to up their production levels without necessarily having to spend more in the process.
Therefore more efficiency and throughput dust grinders should be incorporated into the line and to ensure the right capacities are balanced. This helps to maintain a flow of processing line without overloading the grinders or other equipment like magnetic separators that may be applied in the processing line. The use of technologies including the automated feed system and control software enable clinging to the right loading conditions to enhance the throughputs while preventing the grinder from wearing out.
Improving the degree of utilization of resources has the danger of reducing the quality of the products produced. Therefore, the intervention repertoire shall be balanced in terms of the time taken and accuracy gained. Many personnel should be taught to relate and interchange more than one process parameter and the effects on grinder productivity and the entire plant performance. This knowledge enables them to come up with the right decisions that increase the throughput rates but at the same time maintain quality.
Energy Consumption
Energy efficiency is another important factor which needs to be taken into consideration while using the dust grinders. The energy used by mineral processing equipment is substantial and therefore utilization of energy efficient equipment such as dust grinders highly affects functional costs. Choosing a molinillo de polvo that has been designed in a way that it will not consume a lot of energy means that the plant will be helping the environment by emitting less carbon dioxide and at the same time, the expenses of the plant regarding energy bills will be cut down.
Measures to enhance efficiency involve workable ways through which grinding can be achieved in the least time possible and energy saving machinery like the efficient motors and drive. In operation, variable frequency drives (VFDs) are used to control the grinder speed in proportion to its real-time processing requirements, hence avoiding wastage of energy.
Also, energy recycling systems can be installed to harvest energy used in the grinding process for reuse. For instance, heat produced in grinding may be utilized for drying of minerals which serve to boost the general efficiency of the energy in the plant. Energy conservation is one of the most effective ways through which facilities can minimize their effects to the environment and at the same time cut some costs hence making their operations more efficient.
Maintenance and Durability
Dust grinders must always be kept in great working condition, so that they can work for an extended period. Preventiveness is very essential in reducing chances of breakdown, which are unproductive in terms of flow of production. Strong and properly maintained dust grinders are able to stand up to the challenges that are posed by the mineral processing discipline where usually very hard and abrasive materials are dealt with.
The proactive schedule of maintenance should comprise of regular inspections as well as following a fixed pattern for replacement of wear and tear parts such as grinding media and liners. If the right methods of prognosis and condition monitoring, including vibration analysis, thermal imaging, and similar approaches, are used, it will become possible to observe problems before their manifestations that may lead to harm or shut down the equipment. This kind of proactive maintenance not only adds more years of useful life span to the piece of equipment, but also preserves the ability of the equipment to produce the required throughput.
Also important is the choice of the materials and the technologies with the use of which the dust grinders’ structural durability could be improved. Materials and coatings that can withstand abrasion and corrosion but used in grinder parts, can enable the duration between two replacements to be long, hence cutting costs. Plants spend considerable amounts of money in procuring quality materials and regular maintenance programs and it is a good strategy to avoid the numerous failures in the grinders that usually come hand in hand with high production downtimes.
Integration with Separation Equipment
Some of the critical unit operations involve the combination of dust grinders with magnetic separators such as separadores magneticos that are vital in enhancing effective flows of operations in the mineral processing chain. In this manner and as a result, of an effective integration of the comminution circuit, the finely ground mineral particles are well processed by the separation equipment resulting in minimum losses and maximum recovery.
More attention must be paid to the accommodation of the molinillo de polvo with the separadores magneticos with regards to accommodation and interfacing in particular. Integration of these processes should be done in such a way that there are minimal transition and handling stages where losses or contamination of the material can happen. Furthermore, the various operational processes of the grinder must be coordinated with the magnetic separators, the finished product produced by the grinder must be in the correct form so that it can effectively go through the magnetic separators.
Since these units are closely related, operators can make adjustments to the interconnectivity between these units to optimize the overall performance of the system, increase the amount of flow per unit, and increase recovery efficiency at the same time as reducing the operational costs. Additionally, information, which is gathered from the primary and the second system, can be used for refining the grinding and the separation processes, the integration is not only mechanical but also informational.
In conclusion, dust grinder is among the vital tools utilized in the operation of the mineral processing industry especially when they are accompanied with some of the separation technologies such separadores magneticos. Therefore, the comprehension of the particle size distribution, efficiency, energy consummation, maintenance, and integration of hydrocyclones with separation equipment will help the operator to improve the productivity and profitability of the mineral processing plant. Such factors enable dust grinders to be useful in the mining process to improve processing and help in the realization of economic and production objectives.