Ensuring Safety: Maintenance of Mats
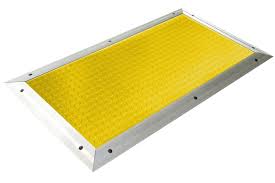
Regular maintenance is a cornerstone of operational efficiency and safety in any facility, whether it be a manufacturing plant, a commercial kitchen, or a healthcare environment. The significance of routine maintenance cannot be overstated; it serves as a proactive measure to prevent equipment failure, reduce downtime, and extend the lifespan of machinery and infrastructure. For instance, in a manufacturing setting, neglecting regular maintenance can lead to catastrophic equipment breakdowns, resulting in costly repairs and lost productivity.
A well-maintained facility not only operates more smoothly but also fosters a culture of safety and responsibility among employees. Moreover, regular maintenance plays a critical role in ensuring compliance with industry standards and regulations. Many sectors are governed by strict guidelines that mandate the upkeep of equipment and facilities to safeguard public health and safety.
For example, in the food service industry, regular maintenance of kitchen equipment is essential to prevent foodborne illnesses. Equipment that is not properly maintained can harbor bacteria and other pathogens, posing significant health risks to consumers. By adhering to a rigorous maintenance schedule, businesses can mitigate these risks and demonstrate their commitment to quality and safety.
Inspection and Repair Procedures
Systematic Checks for Early Detection
In an industrial setting, routine inspections might include checking for wear and tear on machinery, assessing the condition of safety equipment, and ensuring that all systems are functioning as intended. By implementing a structured inspection protocol for warehouse safety mats, organizations can catch minor issues early on, allowing for timely repairs that prevent costly downtime.
Standardized Repair Process
The repair process itself should be well-documented and standardized to ensure consistency and quality. This includes maintaining detailed records of inspections, repairs performed, and any parts replaced. For instance, if a conveyor belt in a manufacturing line shows signs of wear during an inspection, the repair team should not only replace the belt but also document the specific reasons for the replacement and any observations made during the inspection.
Data-Driven Maintenance Planning
This data can be invaluable for future maintenance planning and can help identify patterns that may indicate larger systemic issues within the facility. By analyzing inspection and repair data, organizations can refine their maintenance strategy, optimize resource allocation, and improve overall operational efficiency.
Cleaning and Sanitization Protocols
Cleaning and sanitization protocols are essential for maintaining a safe and healthy environment in any facility. These protocols go beyond mere surface cleaning; they involve comprehensive strategies designed to eliminate contaminants and prevent the spread of pathogens. In healthcare settings, for example, rigorous cleaning protocols are critical to preventing hospital-acquired infections (HAIs).
This includes not only daily cleaning of surfaces but also deep cleaning procedures that target high-touch areas such as doorknobs, light switches, and medical equipment. In food service environments, cleaning protocols must adhere to strict guidelines set forth by health authorities. This includes regular sanitization of kitchen surfaces, utensils, and equipment to prevent cross-contamination.
For instance, after preparing raw meat, all surfaces must be thoroughly cleaned and sanitized before any other food items are prepared. The use of appropriate cleaning agents and techniques is crucial; facilities must ensure that staff are trained in the correct methods to effectively eliminate harmful bacteria while also being mindful of food safety standards.
Storage and Handling Guidelines
Proper storage and handling guidelines are vital for maintaining the integrity of materials and products within any facility. In warehouses or manufacturing plants, improper storage can lead to damage or degradation of materials, resulting in financial losses and operational inefficiencies. For example, chemicals must be stored according to their specific requirements—some may need to be kept at certain temperatures or away from direct sunlight to prevent reactions that could compromise their effectiveness or safety.
In addition to materials, the handling of products during storage is equally important. Employees must be trained in proper lifting techniques to avoid injuries and ensure that products are not damaged during movement. For instance, when handling fragile items such as glassware or electronic components, staff should use appropriate protective gear and follow specific protocols to minimize the risk of breakage.
Implementing clear labeling systems for storage areas can also enhance organization and efficiency, making it easier for staff to locate items quickly while reducing the likelihood of accidents.
Training and Education for Staff
Training and education for staff are critical components of any successful maintenance program. Employees must be equipped with the knowledge and skills necessary to perform their duties effectively while adhering to safety protocols. Regular training sessions can cover a wide range of topics, from equipment operation to emergency response procedures.
For instance, in a manufacturing environment, operators should receive comprehensive training on how to use machinery safely and efficiently, including understanding the importance of regular maintenance checks. Furthermore, ongoing education is essential for keeping staff updated on new technologies and best practices within their industry. As equipment evolves and regulations change, it is crucial that employees remain informed about the latest developments that could impact their work.
For example, if a new piece of machinery is introduced that incorporates advanced safety features, staff should receive training on how to utilize these features effectively. This not only enhances operational efficiency but also fosters a culture of continuous improvement within the organization.
Compliance with Safety Standards and Regulations
Compliance with safety standards and regulations is non-negotiable in any industry where public health and safety are at stake. Regulatory bodies establish guidelines that organizations must follow to ensure safe operations; failure to comply can result in severe penalties, including fines or even closure. For instance, in the construction industry, adherence to Occupational Safety and Health Administration (OSHA) regulations is critical for protecting workers from hazards such as falls or exposure to harmful substances.
To maintain compliance, organizations must implement robust systems for monitoring adherence to workplace safety standards. This includes conducting regular audits and inspections to assess compliance levels across various departments. For example, a food processing plant may undergo routine inspections by health authorities to ensure that sanitation practices meet regulatory requirements.
By proactively addressing any deficiencies identified during these inspections, organizations can not only avoid penalties but also enhance their reputation as responsible operators committed to safety. In conclusion, the multifaceted approach to maintenance—encompassing regular upkeep, thorough inspections, effective cleaning protocols, proper storage practices, comprehensive training for staff, and strict compliance with safety regulations—forms the backbone of operational excellence in any facility. Each element plays a vital role in creating an environment that prioritizes safety, efficiency, and quality.
By investing in these areas, organizations can ensure long-term success while safeguarding the well-being of their employees and customers alike.