Exploring Non-Conversion Coating Types, Thermoplastic Coating, and Polymer Coating Types
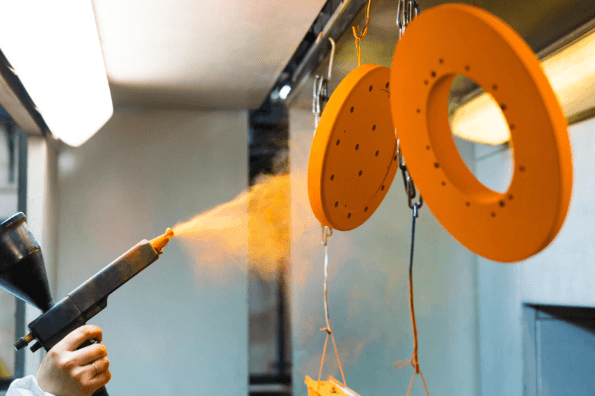
In the coatings’ industry, understanding the various types of coatings is vital for selecting the right solution for specific applications. This article will delve into non-conversion coating types, thermoplastic coatings, and volatile coatings, while also examining different polymer coating types and the characteristics of various paint polymer types.
Non-Conversion Coating Types vs. Thermoplastic Coating and Volatile Coatings
Non-conversion coatings are coatings that do not undergo a chemical change during the curing process. Instead, they adhere to the surface through physical means. Common examples include acrylics, polyurethanes, and epoxy coatings that are often used for protective and decorative purposes.
When comparing Non-Conversion Coating Types vs. Thermoplastic Coating and Volatile Coatings, it’s important to note that thermoplastic coatings, unlike non-conversion coatings, can be melted and reshaped with heat. Volatile coatings, on the other hand, release solvents during curing, which can affect environmental and health safety considerations. Understanding these differences helps in selecting the appropriate coating based on the specific application requirements.
- Non-Conversion Coating Types: These coatings remain unchanged during application, making them easy to use and remove. They are ideal for temporary applications or environments where the surface will undergo minimal wear and tear.
- Thermoplastic Coatings: In contrast, thermoplastic coatings are designed to soften when heated and harden upon cooling, allowing for re-melting and reapplication. These coatings are typically made from materials such as polyethylene, polypropylene, and polyvinyl chloride (PVC). Their ability to be reshaped under heat makes them suitable for applications that require flexibility and the possibility of repairs or modifications.
- Volatile Coatings: Volatile coatings contain solvents that evaporate during the curing process, leaving behind a solid coating. These coatings are commonly used in paints and sealants. While they provide a smooth finish, their high levels of volatile organic compounds (VOCs) can contribute to environmental concerns and health issues.
Understanding these distinctions is crucial for selecting the appropriate coating for your project. Non-conversion coatings offer ease of application, while thermoplastic coatings provide flexibility and repairability. Volatile coatings, while effective, require careful handling due to potential environmental impacts.
See also: A Comprehensive Guide to Replacement for Harvey Windows: Exploring Top Alternatives
Polymer Coating Types and Different Paint Polymer Types
Polymer coatings are widely used in various industries for their protective properties, aesthetic appeal, and durability. They can be categorized into several types, each with distinct characteristics and applications. When comparing Polymer Coating Types and Different Paint Polymer Types, it’s essential to understand that each type of polymer, whether it’s acrylic, epoxy, or polyurethane, brings unique properties to the coating. For this reason, acrylic polymers are often chosen for their quick-drying nature and UV resistance, while epoxy coatings are prized for their strong adhesion and chemical resistance. These variations allow for tailored solutions depending on the specific needs of the surface and environment.
- Acrylic Coatings: Known for their excellent clarity and resistance to UV light, acrylic coatings are often used in outdoor applications. They provide a durable finish and are available in various formulations for different uses.
- Epoxy Coatings: These coatings are renowned for their strong adhesion and chemical resistance, making them ideal for industrial applications. Epoxy coatings are often used in flooring, marine, and automotive industries due to their durability and protective qualities.
- Polyurethane Coatings: Polyurethane coatings offer flexibility and abrasion resistance, making them suitable for a wide range of applications, including automotive finishes and industrial machinery. They are available in both water-based and solvent-based formulations.
- Silicone Coatings: These coatings are used for high-temperature applications due to their ability to withstand extreme heat. Silicone coatings provide excellent weather resistance and are commonly used in roofing and automotive applications.
- Polyester Coatings: Known for their excellent color retention and gloss, polyester coatings are often used in exterior applications where aesthetics are a priority. They are resistant to fading and chalking, making them suitable for outdoor furniture and fixtures.
- Vinyl Coatings: Vinyl coatings are often used for their flexibility and impact resistance. They are commonly applied to automotive and industrial surfaces, providing a durable and protective finish.
Each paint polymer type offers unique benefits, making it important to select the right one based on the specific requirements of the project. Factors to consider include environmental exposure, desired aesthetic finish, and chemical resistance.
Conclusion
In summary, understanding the differences between non-conversion coating types, thermoplastic coatings, and volatile coatings is essential for selecting the right coating for specific applications. Each type of coating has its advantages and limitations, influencing performance and suitability. Furthermore, familiarity with various polymer coating types and paint polymer types enables informed decision-making, ensuring optimal protection and aesthetic appeal for coated surfaces. By carefully considering these factors, industries can enhance the longevity and effectiveness of their coatings, leading to improved performance in various environments.